Introduction
In the ever-evolving landscape of metal fabrication, innovation is key to staying competitive. The introduction of advanced technologies has revolutionized traditional methods, with laser cutting taking center stage. Among these innovations, the laser pipe cutting machine stands out as a game-changer, offering precision and efficiency that were once thought impossible.
Revolutionizing Metal Fabrication
The advent of pipe laser cutting technology has transformed how industries approach metal fabrication. Gone are the days of labor-intensive processes; today’s laser machines streamline operations and enhance productivity. With their ability to deliver intricate designs and flawless cuts, these machines are redefining what is possible in metalworking.
The Need for Precision in Cutting
Precision is paramount in any cutting operation, especially when it comes to intricate designs or critical applications. Traditional cutting methods often fall short, leading to wastage and increased costs due to errors. Laser cutting machines eliminate these issues by providing unparalleled accuracy, ensuring that every cut meets exact specifications without compromise.
What is a Laser Pipe Cutting Machine?
A laser pipe cutting machine utilizes focused beams of light to slice through various materials with remarkable precision. Unlike conventional tools that rely on physical force, this innovative technology harnesses the power of lasers for clean and efficient cuts. By integrating a sophisticated control system with advanced optics, these machines can handle complex shapes and sizes while maintaining high-speed performance.
Understanding Pipe Laser Cutting Technology
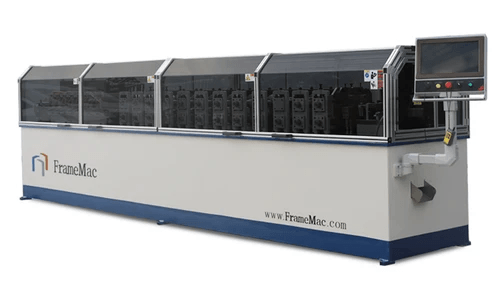
Laser cutting technology has transformed the landscape of metal fabrication, particularly in the realm of pipe laser cutting. This advanced method uses focused beams of light to slice through materials with unparalleled precision, allowing for intricate designs and clean edges that traditional methods often struggle to achieve. Understanding how this technology works is crucial for anyone looking to invest in a laser machine.
The Mechanics Behind Laser Cutting
At its core, a laser cutting machine operates by directing a high-powered beam of light onto the surface of the material being cut. This concentrated energy heats the metal until it melts or vaporizes, effectively creating a clean cut without excessive force or physical contact. The precision of this process is enhanced by computer numerical control (CNC), which allows for exact measurements and repeatable results, making it ideal for complex pipe laser cutting tasks.
Advantages of Laser Cutting Over Traditional Methods
When comparing laser cutting to traditional methods like plasma or mechanical cutting, several key advantages emerge. For starters, laser machines provide higher accuracy and finer cuts, reducing the need for secondary finishing processes that can add time and cost to projects. Additionally, they offer greater versatility; whether it's thick steel or thin aluminum, a laser pipe cutting machine can handle various materials with ease while minimizing waste.
Key Components of a Laser Cutting Machine
A typical laser cutting machine consists of several essential components that work together seamlessly to deliver superior results. These include the laser source—often a fiber or CO2 laser—which generates the beam; optics that focus and direct the beam onto the workpiece; and motion systems that control movement along multiple axes for intricate designs. Each part plays a vital role in ensuring efficient operation and optimal performance during pipe laser cutting processes.
The Role of Automatic Feeding Systems
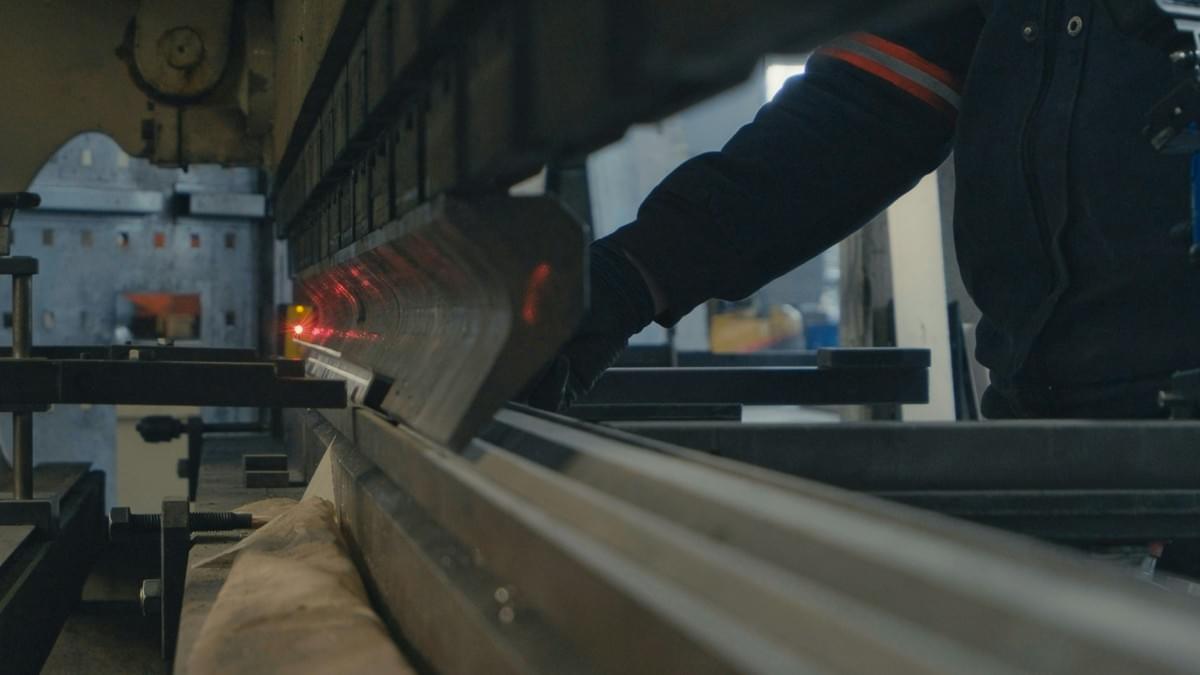
In the fast-paced world of metal fabrication, efficiency is king. Automatic feeding systems play a pivotal role in enhancing the overall productivity of laser pipe cutting machines. By automating the process of material handling, these systems minimize downtime and ensure that the laser cutting machine operates at peak performance.
How Automatic Feeding Enhances Efficiency
Automatic feeding systems streamline the workflow by continuously supplying material to the laser cutting machine without manual intervention. This not only accelerates production but also reduces human error, ensuring that each cut is precise and consistent. With less time spent on loading and unloading materials, operators can focus on other critical tasks, ultimately boosting throughput in pipe laser cutting operations.
Moreover, these systems can be programmed to handle various sizes and types of materials with ease, allowing for quick adjustments between different projects. This versatility means that businesses can adapt to changing demands without sacrificing quality or speed in their laser cutting processes. In essence, automatic feeding transforms traditional metal cutting practices into a well-oiled machine where efficiency reigns supreme.
Types of Automatic Feeding Systems Available
When it comes to automatic feeding systems for laser machines, there are several options available to suit different operational needs. One popular type is the roll feeder, which unwinds coils of metal and feeds them directly into the laser cutting machine for seamless operation. Another option is the sheet feeder that handles flat sheets efficiently while maintaining precision during cuts.
Additionally, some advanced systems incorporate sensors that detect material size and automatically adjust settings accordingly—talk about smart technology! These innovations not only enhance accuracy but also minimize waste during pipe laser cutting processes by ensuring each piece is utilized effectively. With so many choices on offer, businesses can select an automatic feeding system tailored to their specific requirements.
Integration with Laser Cutting Machines
Integrating automatic feeding systems with laser cutting machines creates a harmonious workflow where every component works together efficiently. Modern laser machines are designed to accommodate these automated feeders seamlessly, allowing for real-time communication between devices for optimal performance. This integration ensures that as soon as one batch is completed in the cutting process, another batch is already being prepared for immediate processing.
Furthermore, advanced software solutions enable operators to monitor both the feeding system and the laser machine from a single interface—making it easier than ever to manage production schedules and inventory levels effectively. By combining automatic feeding with state-of-the-art pipe laser cutting technology, manufacturers can achieve unprecedented levels of precision while maximizing output efficiency across their operations.
Applications of Laser Cutting Machines
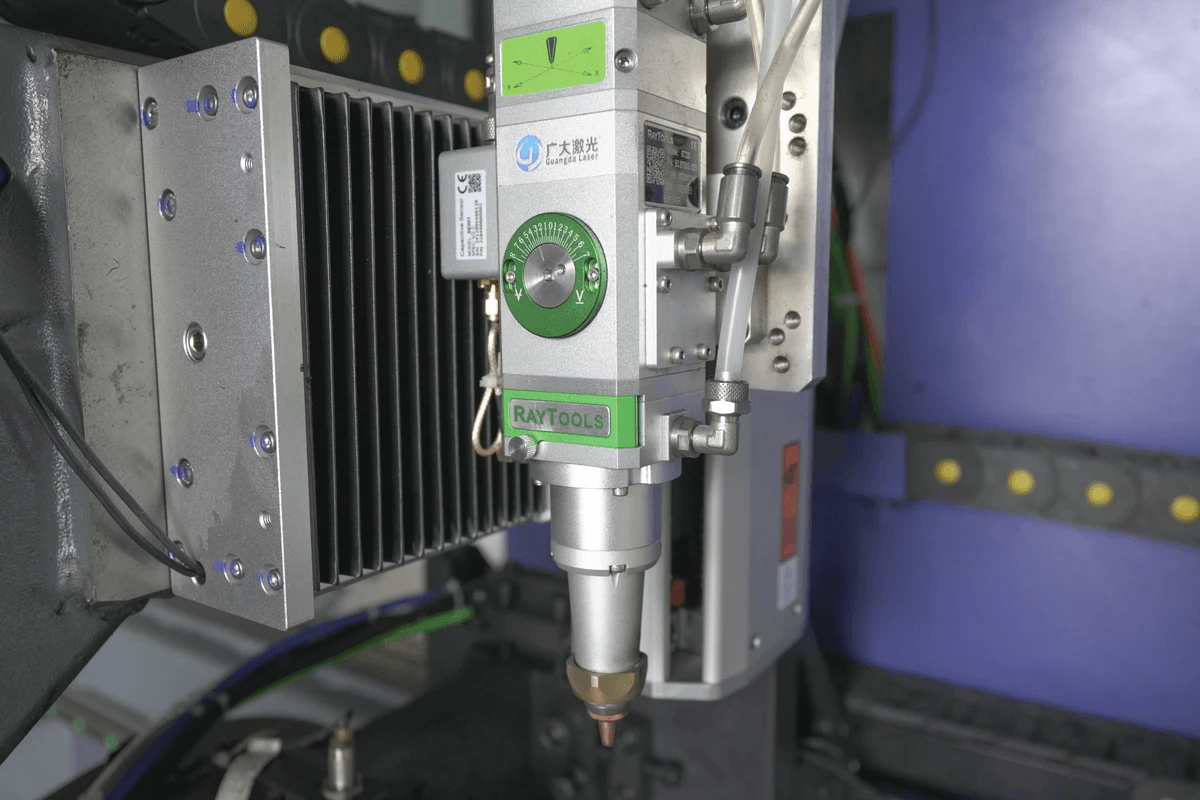
Laser cutting machines have transformed various industries by introducing unparalleled precision and efficiency in metal fabrication. One of the standout technologies in this realm is the laser pipe cutting machine, which excels at delivering clean and accurate cuts for a wide range of materials. From automotive to aerospace, the applications of pipe laser cutting are both diverse and impactful.
Industries Benefiting from Laser Pipe Cutting
The automotive industry has been one of the primary beneficiaries of laser cutting technology, utilizing laser machines for everything from exhaust systems to intricate chassis components. In construction, laser cutting allows for precise fabrication of steel pipes and frames, ensuring structural integrity while reducing waste. Additionally, sectors such as HVAC and plumbing rely heavily on pipe laser cutting to create customized solutions that meet specific project requirements.
Manufacturers across these industries appreciate how laser cutting enhances production speed while maintaining high-quality standards. The ability to cut various materials with precision means fewer errors and less rework, leading to significant cost savings over time. Moreover, as industries increasingly prioritize sustainability, the efficiency of laser machines helps minimize material waste—a win-win for both business and environment.
Customization Capabilities with Laser Technology
One of the most compelling advantages of using a laser machine is its exceptional customization capabilities. Unlike traditional methods that may require extensive tooling changes or setups, a pipe laser cutting machine can be programmed to execute complex designs with ease. This flexibility allows manufacturers to cater to unique client specifications without sacrificing speed or quality.
The adaptability of laser technology also extends to different materials—whether it’s stainless steel, aluminum, or even plastic pipes—laser cutting can handle it all without compromising on precision. This versatility makes it an ideal choice for companies looking to offer bespoke solutions tailored specifically for their customers' needs. Additionally, rapid prototyping becomes feasible; businesses can quickly turn ideas into tangible products through efficient design iterations.
Case Studies of Successful Implementations
Consider a leading automotive manufacturer that recently integrated a state-of-the-art pipe laser cutting machine into its production line. By doing so, they reduced their manufacturing time by 30% while increasing accuracy in their exhaust system components—a critical factor in meeting stringent emission standards. This transition not only boosted productivity but also enhanced product reliability.
Another notable example comes from an HVAC company that faced challenges with custom ductwork fabrication due to varying client demands. After adopting advanced laser cutting technology, they were able to streamline operations significantly while providing tailored solutions faster than ever before—resulting in improved customer satisfaction rates and repeat business opportunities.
These case studies illustrate how embracing innovative technologies like pipe laser cutting can lead to remarkable improvements in operational efficiency and product quality across various sectors.
Choosing the Right Laser Cutting Machine
Selecting the right laser cutting machine is crucial for any business aiming to enhance its metal fabrication capabilities. With a plethora of options available, it’s essential to identify which features align with your specific needs. Investing in a quality pipe laser cutting machine can significantly boost efficiency, precision, and overall productivity.
Key Features to Look For
When evaluating a laser cutting machine, several key features should be at the forefront of your decision-making process. First and foremost, consider the power output; higher wattage typically translates to faster cutting speeds and the ability to handle thicker materials. Additionally, look for advanced software compatibility that allows for easy integration with design programs and offers customization options for intricate designs in pipe laser cutting.
Another essential feature is the type of laser used; CO2 lasers are excellent for non-metal materials, while fiber lasers excel in cutting metal efficiently. Furthermore, assess the machine's automation capabilities—automatic feeding systems can drastically reduce downtime and enhance workflow efficiency during production runs. Lastly, ensure that safety features are robust; a reliable laser machine should prioritize operator safety without compromising performance.
Comparison of Leading Brands
With numerous brands dominating the market, comparing their offerings can help you make an informed choice when selecting your laser pipe cutting machine. Companies like Trumpf and Bystronic are well-known for their high-quality machines that combine speed with precision in metal cutting applications. On the other hand, brands like Amada focus on providing versatile solutions tailored specifically for various industries.
Price points vary significantly among leading brands; however, it's essential to balance cost with quality and functionality when making your decision. Some manufacturers might offer budget-friendly options but could lack advanced features or support services that could be critical down the line. Therefore, conducting thorough research on brand reputation through customer reviews and case studies can provide valuable insights into which brand aligns best with your needs.
Importance of Manufacturer Support
Choosing a reputable manufacturer goes beyond just purchasing a laser cutting machine; ongoing support is crucial for maximizing your investment's value over time. A strong support system ensures you have access to technical assistance whenever required—this includes troubleshooting issues or receiving training on new features of your pipe laser cutting equipment. Companies that provide comprehensive training services empower operators to utilize their machines effectively from day one.
Moreover, consider manufacturers who offer extended warranties or service contracts; this can save significant costs associated with repairs or maintenance down the line while ensuring consistent performance from your equipment. Establishing a relationship with your manufacturer fosters trust and reliability—critical elements when navigating any challenges that may arise during operation or production scaling efforts.
Kiant Machinery: Your Partner in Laser Cutting
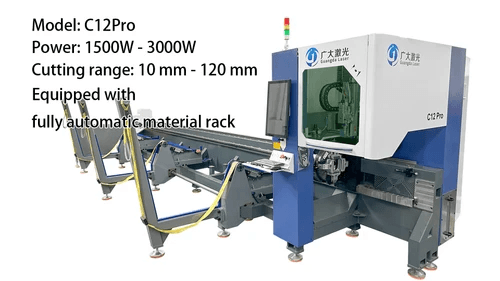
In the rapidly evolving world of metal fabrication, Kiant Machinery stands out as a leader in providing innovative solutions tailored specifically for laser cutting applications. Their state-of-the-art laser machines are designed to meet the diverse needs of industries that rely on precision and efficiency, particularly in pipe laser cutting. With a commitment to quality and performance, Kiant Machinery has positioned itself as a trusted partner for businesses looking to enhance their metal cutting capabilities.
Innovative Solutions for Metal Fabrication
Kiant Machinery offers an impressive range of laser cutting machines that cater to various metal fabrication needs. From high-speed cutting lasers to robust laser pipe cutting machines, their products are engineered for accuracy and reliability. These innovative solutions not only improve the quality of cuts but also significantly reduce operational costs through enhanced productivity.
The technology behind these laser machines is continuously evolving, ensuring that clients benefit from the latest advancements in pipe laser cutting technology. By integrating features such as automated settings and real-time monitoring systems, Kiant's machines provide users with unparalleled control over their operations. This level of innovation allows businesses to push boundaries and explore new possibilities in metal fabrication.
Comprehensive Support and Training Services
Kiant Machinery understands that investing in a laser machine is just the beginning; ongoing support is crucial for maximizing its potential. That’s why they offer comprehensive training services aimed at helping clients fully understand the capabilities of their new equipment. From hands-on training sessions to detailed user manuals, customers are equipped with all necessary skills to operate their laser cutting systems efficiently.
Moreover, Kiant provides dedicated customer support teams ready to assist with any technical questions or challenges that may arise post-purchase. This commitment ensures that your investment translates into tangible results without unnecessary downtime or frustration. With Kiant's support by your side, you can confidently navigate the world of cutting laser metal applications.
Success Stories from Kiant Machinery Clients
Over the years, numerous clients have shared success stories illustrating how Kiant Machinery's products transformed their operations through advanced pipe laser cutting technology. One notable case involved a manufacturing firm that upgraded its traditional methods with a state-of-the-art laser machine from Kiant; within months, they reported increased production speed and reduced waste material significantly. The precision offered by their new equipment allowed them to take on more complex projects while maintaining high-quality standards.
Another client specializing in custom metalwork found that integrating an automatic feeding system with their new laser machine revolutionized their workflow efficiency—allowing them to handle larger orders without sacrificing accuracy or lead times. These testimonials not only highlight the effectiveness of Kiant’s solutions but also emphasize how investing in modern technology can yield substantial returns for businesses across various sectors.
Conclusion
In the rapidly evolving landscape of metal fabrication, the future of cutting technology is bright and full of promise. As industries continue to demand higher precision and efficiency, innovations in pipe laser cutting are setting new standards for what’s possible. The continuous advancements in laser machine technology will likely lead to even more sophisticated applications and capabilities, making it an exciting time for manufacturers and fabricators alike.
The Future of Metal Cutting Technology
The future of metal cutting technology is poised to embrace further integration with automation and artificial intelligence. Laser cutting machines are already becoming smarter, with features that allow for real-time monitoring and adjustments during the cutting process. This not only enhances precision but also streamlines operations, making laser pipe cutting the go-to choice for many industries looking to stay competitive.
Investing in Efficiency and Precision
Investing in a laser machine is not just about acquiring a tool; it's about embracing a philosophy of efficiency and precision that can transform production processes. The initial cost may seem daunting, but the long-term benefits—such as reduced waste, faster turnaround times, and superior quality—far outweigh any upfront investment. Companies that prioritize modern solutions like laser cutting will find themselves reaping rewards in productivity and profitability.
Final Thoughts on Laser Pipe Cutting Machines
In conclusion, laser pipe cutting machines represent a significant leap forward in metal fabrication technology. With their unparalleled accuracy and versatility, they cater to diverse industries while enabling customization at unprecedented levels. As businesses look toward the future, adopting this advanced technology will be crucial for staying ahead of the curve in an ever-competitive market.